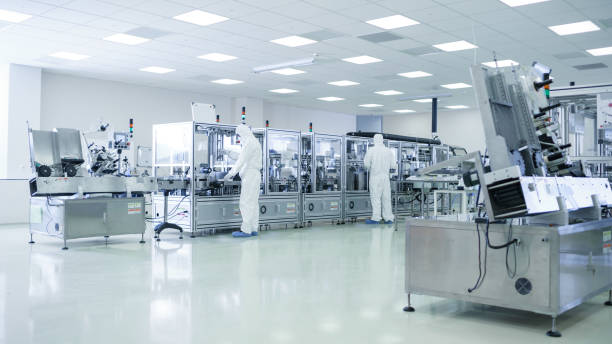
When you think of 3D printing, you might picture household gadgets, prototypes, or maybe even miniatures. But did you know it’s also making waves in industries like aerospace? Yep, 3D printing in aerospace is no longer just a futuristic dream—it’s a reality that’s already starting to take off. From creating lightweight components to custom tools, 3D printing is helping aerospace companies push the limits of what’s possible. Here’s a closer look at how 3D printed parts are being used in this high-stakes industry.
Materials Matter: Why 3D Printing Works for Aerospace
In the aerospace world, strength, durability, and weight are crucial. That’s why aerospace 3D printing uses some pretty advanced materials like titanium and high-temperature resistant polymers. These materials are not only tough but also lightweight—making them perfect for parts that need to perform under extreme conditions without adding unnecessary weight. Whether it’s engine components or specialized tools, 3D printing can produce these parts with precision and strength that traditional manufacturing methods can’t always match.
Applications: How 3D Printing is Changing Aerospace
So, what exactly are aerospace companies printing? Well, the possibilities are pretty exciting:
- Prototypes: 3D printing is ideal for rapid prototyping, allowing engineers to quickly design and test new parts or products before committing to mass production. This cuts down on development time and costs.
- Lightweight Structural Parts: One of the biggest challenges in aerospace is reducing weight without sacrificing strength. 3D printing makes it possible to create intricate parts that are both lightweight and durable, which is a game-changer for everything from aircraft to rockets.
- Custom Tools: Need a tool that’s tailor-made for a specific task? 3D printing is perfect for creating custom jigs, fixtures, and tools that are built to exact specifications.
The ability to produce highly complex and lightweight parts means aerospace engineers can design more efficient and innovative machines—everything from airplanes to spacecraft.
Challenges: The Hurdles We Still Face
Of course, it’s not all smooth sailing. While 3D printing has tons of potential, there are still some challenges to overcome:
- Regulations: Aerospace is one of the most highly regulated industries in the world, and 3D printed parts need to meet strict safety standards. Getting the parts certified can be a lengthy and costly process, but it’s essential to ensure they’re safe to use in such high-risk environments.
- Quality Control: Ensuring consistency and reliability across 3D printed parts is another hurdle. The aerospace industry can’t afford to have any defective components, so 3D printing processes need to be highly refined to meet the necessary quality standards.
Despite these challenges, the potential for 3D printing in aerospace is immense, and it’s only a matter of time before we see even more widespread adoption.
The Bottom Line: 3D Printing is Taking Off in Aerospace
So, can 3D printed parts be used in aerospace? Absolutely! Whether it’s for prototypes, lightweight components, or custom tools, 3D printing is revolutionizing how things are made in the aerospace industry. With materials like titanium and heat-resistant polymers, aerospace companies are creating parts that are stronger, lighter, and more precise than ever before.
If you’re working in aerospace or just interested in the possibilities of 3D printing in high-tech industries, this is an exciting space to watch. And who knows—someday, the technology could be helping build the next generation of spacecraft or even 3D printing parts for Mars exploration!