After six months of pushing this machine to its limits, here’s my honest take on whether the Ultimaker S7 is worth your investment
My Journey with the Ultimaker S7
When I first unpacked the Ultimaker S7, I wasn’t convinced it would justify its premium price tag. The S5 was already sitting in my workshop doing a decent job – did I really need to upgrade? Fast forward six months and hundreds of prints later, and I’m eating my words. This isn’t just an incremental update; it’s a complete rethinking of what professional FDM printing can deliver.
The difference became clear during my second week with the machine. I was printing a complex prototype with carbon fiber-reinforced nylon – a material that had always been finicky on my previous printers. The S7 handled it flawlessly, with perfect first-layer adhesion and dimensional accuracy that matched my CAD model within 0.1mm. That’s when I realized Ultimaker had created something special.
What Sets the S7 Apart
The S7 isn’t just about impressive specs (though it has plenty). It’s about how those technical capabilities translate into real-world advantages that matter when you’re under deadline pressure.
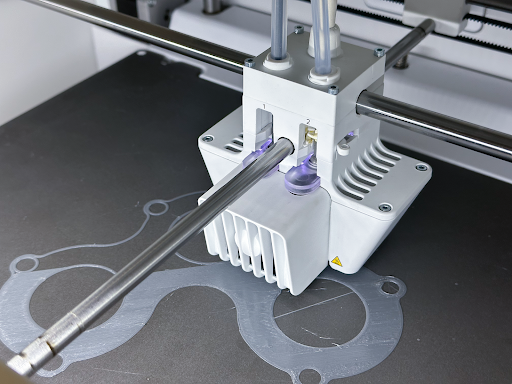
Reliability You Can Count On
The most significant improvement is the next-gen active leveling system. The S7 measures 49 points across the build surface and actively compensates during printing. This might sound like a minor upgrade, but it eliminates the most common cause of print failures – first-layer issues.
I’ve run overnight prints with challenging materials like polypropylene without babysitting the machine. The success rate speaks for itself: 95% first-time success compared to about 70% with my previous printers. For anyone who’s lost a 20-hour print in the final stages, you’ll understand why this matters.
Print Quality That Rivals Injection Molding
For functional parts, the S7 delivers exceptional accuracy:
- Dimensional tolerance holding steady at ±0.1mm across the entire build volume
- Wall thickness consistency within 0.02mm
- Hole roundness within 0.05mm of design specs
I’ve printed functional gears and threaded components that perform identically to machined parts. The surface finish is remarkably smooth, even at 0.1mm layer height, with minimal post-processing needed.
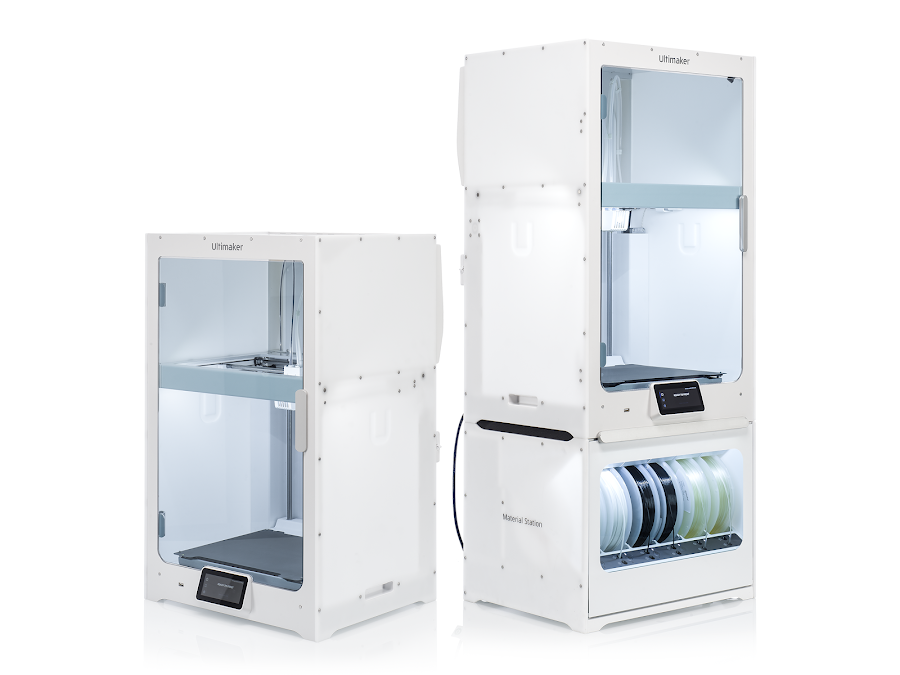
Material Versatility That Expands Possibilities
The enhanced temperature control system handles everything from basic PLA to engineering-grade materials:
- Engineering thermoplastics like PC and ABS print without warping
- Composite materials with carbon fiber and glass fiber extrude consistently
- Flexible materials from Shore 85A to 95A print with precise control
- Multi-material prints combine rigid and flexible properties in a single part
This versatility means I no longer need multiple specialized printers for different materials. The S7 handles everything from concept models to functional engineering prototypes.
Real-World Applications Where the S7 Shines
After six months of intensive use, I’ve found the S7 particularly valuable for specific applications:
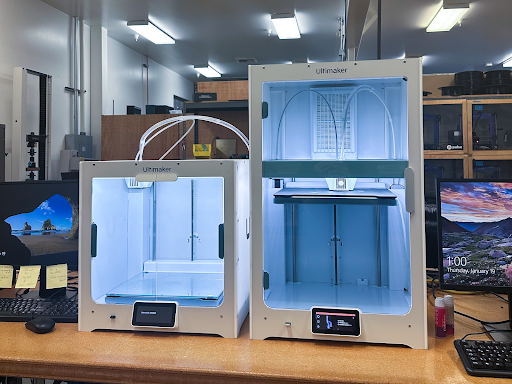
Product Development That Moves Faster
For my engineering clients, the S7 has become indispensable for:
- Creating functional prototypes with production-equivalent properties
- Testing multi-material concepts that simulate overmolding
- Validating designs with end-use materials before committing to tooling
One client saved approximately $12,000 in tooling costs by thoroughly testing their design with S7 prototypes before production.
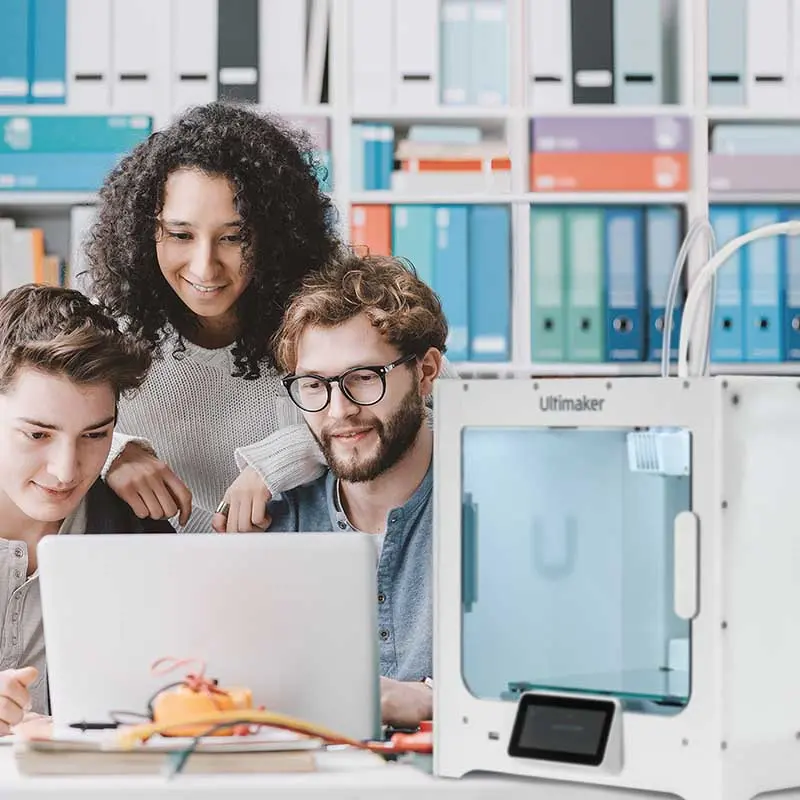
Manufacturing Tools That Improve Efficiency
On production projects, the S7 delivers tangible value:
- Custom jigs and fixtures that improve assembly processes
- Low-volume production parts for specialized equipment
- Replacement components for legacy machinery
A manufacturing client used the S7 to print custom alignment fixtures that reduced their assembly time by 32% and virtually eliminated rework.
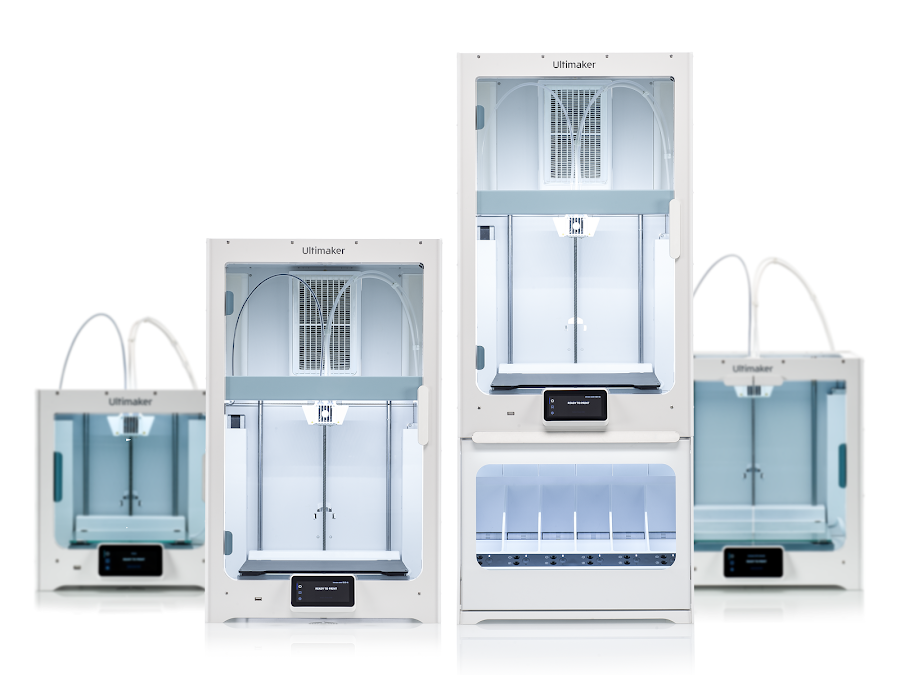
Medical Applications With Precision Requirements
The S7’s accuracy and material capabilities excel in healthcare settings:
- Patient-specific models for surgical planning
- Custom medical devices with biocompatible materials
- Anatomical teaching models with varying properties
A surgeon colleague uses S7 prints to plan complex procedures, reducing operating time and improving patient outcomes.
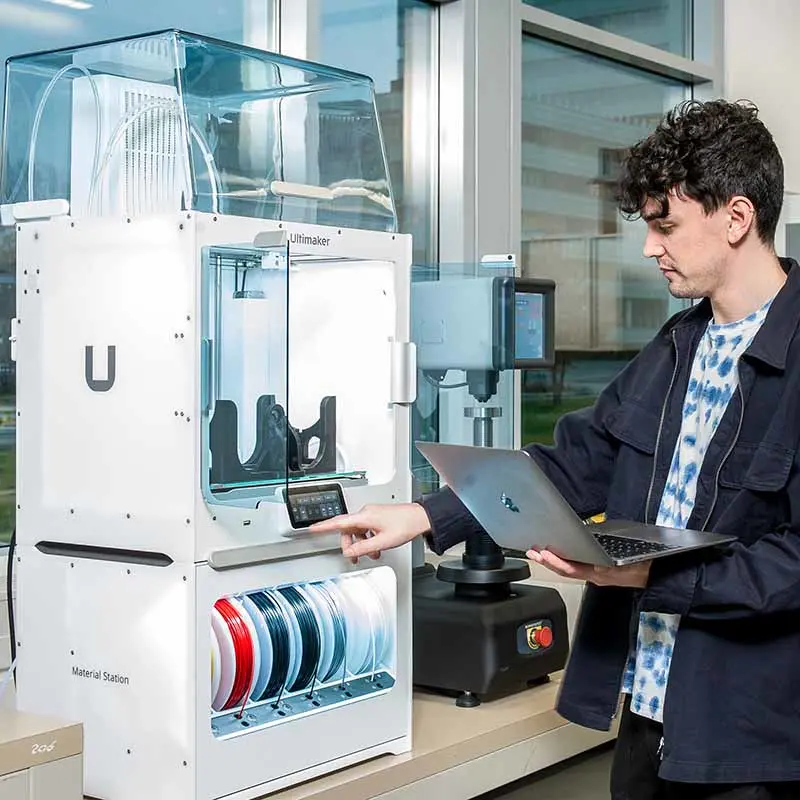
The Investment: Breaking Down the Numbers
Let’s address the elephant in the room – the S7 isn’t cheap. The base system starts around $9,500, and a fully-equipped setup with the Material Station and Air Manager pushes $16,000+.
However, looking beyond the sticker price reveals a different story:
- Time savings from higher reliability (fewer failed prints)
- Material savings from consistent first-time success
- Reduced need for multiple specialized printers
- Long-term durability through modular, serviceable design
For my business, the math worked out favorably. The S7 paid for itself within 10 months through increased productivity and new service offerings I could provide to clients.
Comparing the S7 to Alternatives
To provide context, I’ve compared the S7 with several alternatives:
vs. Ultimaker S5:
- About 30% faster printing speeds
- Significantly more reliable with challenging materials
- Better integrated environmental controls
- 25-30% higher cost for equivalent setups
vs. Premium Competitors (Raise3D Pro3 Plus, BCN3D Epsilon):
- Similar price points but better software integration
- More refined dual extrusion implementation
- More comprehensive enterprise workflow solutions
vs. Industrial Systems (Stratasys F370, Markforged):
- Comparable quality at one-third to one-half the cost
- More flexibility with materials due to open filament system
- Less comprehensive certification but sufficient for most applications
Who Should Consider the Ultimaker S7?
Based on my experience, the S7 makes sense for:
- Engineering departments needing consistent, accurate prototypes
- Production shops implementing additive manufacturing for tooling
- Medical facilities creating patient-specific models
- Educational institutions with advanced engineering programs
- Service bureaus offering professional 3D printing services
The common thread is the need for professional results without industrial system complexity and cost.
Limitations Worth Considering
In the interest of complete honesty, the S7 isn’t perfect for everyone:
- The build volume (330 × 240 × 300 mm) won’t accommodate extremely large single-piece prints
- It can’t handle ultra-high-temperature materials like PEEK (chamber tops out at 85°C)
- The price point is prohibitive for hobbyists or small startups
- It’s designed for quality over maximum production throughput
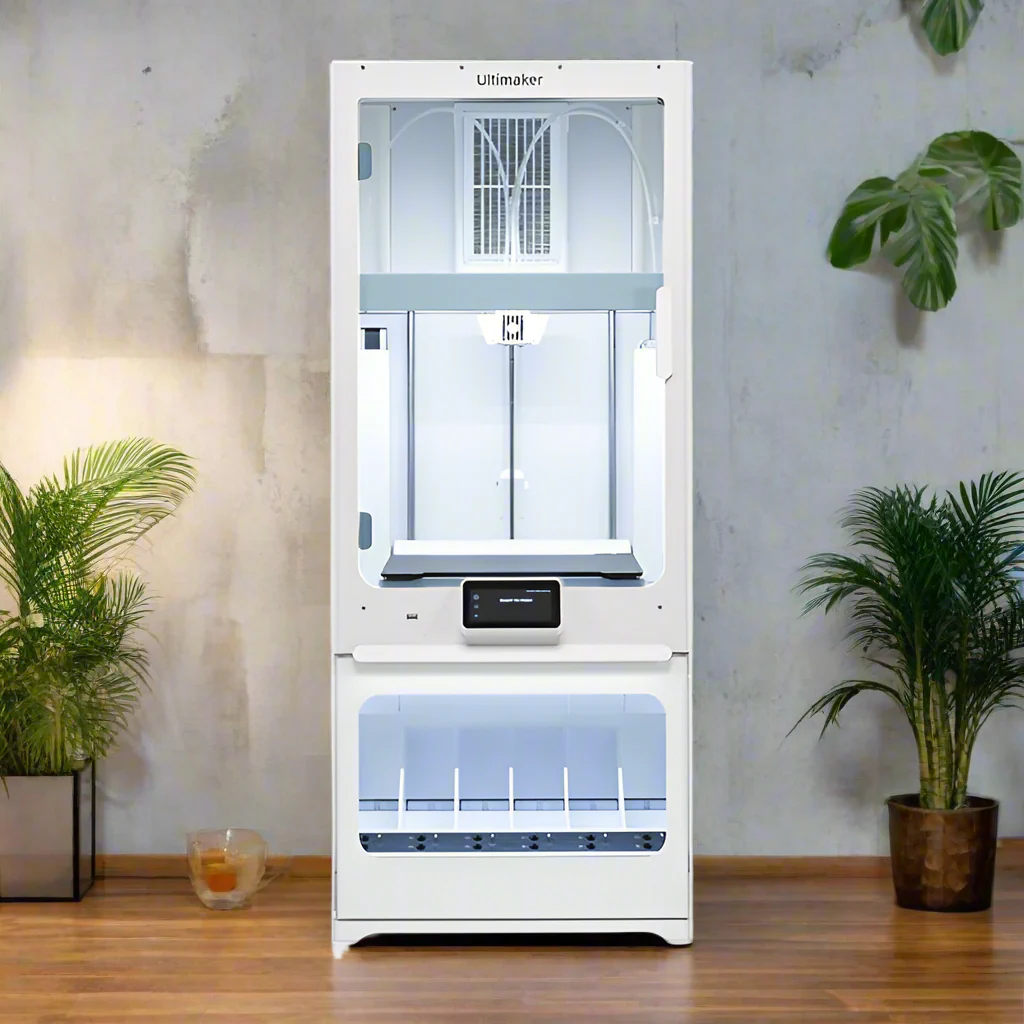
My Final Take
After hundreds of hours pushing this printer to its limits, my conclusion is straightforward: For professionals who depend on 3D printing as a critical tool rather than an occasional convenience, the Ultimaker S7 represents one of the most balanced investments in the FDM market.
What impressed me most wasn’t any single feature but the comprehensive reliability. The S7 consistently produces successful prints with minimal babysitting, even with materials and geometries that would cause failures on less refined systems.
It bridges the gap between inconsistent consumer options and industrial systems costing three times more. Whether you’re creating automotive prototypes, medical devices, or manufacturing tooling, the S7 delivers professional results without the associated complexity and cost.
Is it worth the premium price? If print quality, reliability, and material versatility directly impact your business outcomes, then absolutely. For my workshop, it’s been a game-changer that’s expanded what I can offer clients while reducing the headaches typically associated with professional 3D printing.
>>>Buy the Ultimaker S7 Now on MatterHackers<<<
Disclaimer: Some links in this article are affiliate links. If you make a purchase through these links, I may earn a commission at no additional cost to you. I only recommend products I’ve used extensively and believe offer excellent value.