Commercial 3D Printing: Revolutionizing Industries, Layer By Layer
Commercial 3D printing has rapidly transformed various industries, offering innovative solutions and streamlining production processes. From rapid prototyping to customized manufacturing, the applications are vast and continually evolving. If you’re considering integrating 3D printing into your business or personal projects, selecting the right equipment is crucial. To assist you, we’ve curated a list of top-rated 3D printers and accessories available on Amazon and MatterHackers, each boasting high ratings and numerous reviews.
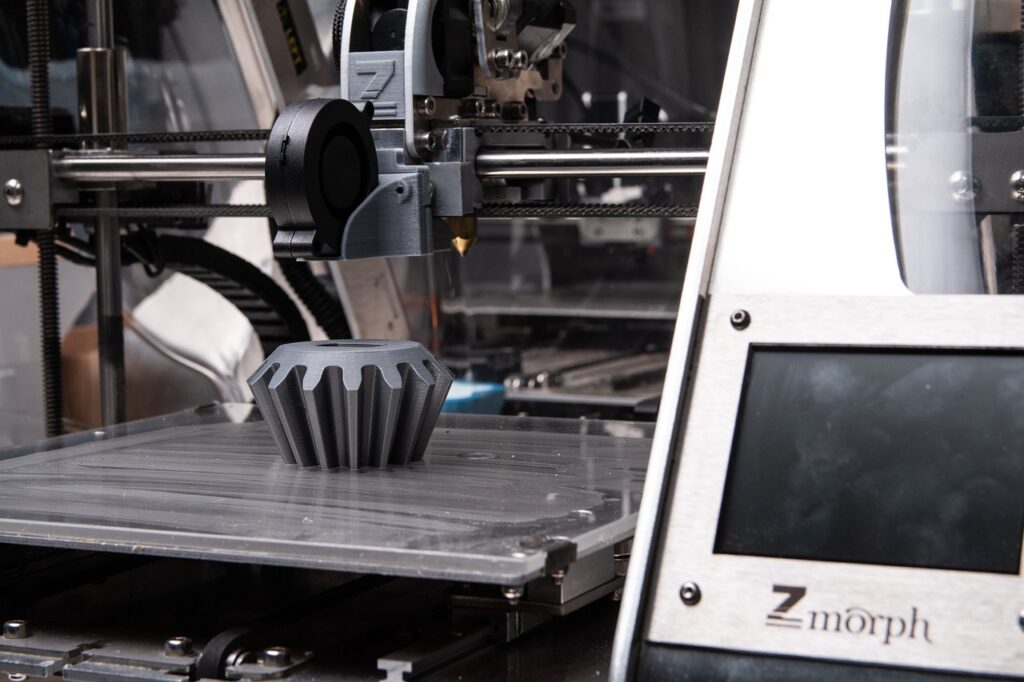
The Evolution of 3D Printing in Commercial Applications
Over the years, 3D printing has expanded beyond hobbyists and small-scale makers to become an essential tool in commercial settings. Industries such as healthcare, aerospace, automotive, and construction have integrated 3D printing technology to enhance efficiency, reduce costs, and accelerate innovation.
- Healthcare: Medical professionals use 3D printing for prosthetics, dental implants, and even bioprinting tissues. This has led to custom solutions tailored to patient needs, improving overall healthcare outcomes.
- Aerospace: Companies like Boeing and SpaceX leverage 3D printing for producing lightweight, complex components that traditional manufacturing methods struggle to create.
- Automotive: The ability to rapidly prototype new vehicle parts enables faster design iterations and production, benefiting manufacturers and aftermarket providers.
- Construction: 3D-printed houses and structures are becoming a reality, reducing construction time and material waste while offering affordable housing solutions.
FLASHFORGE Adventurer 5M 3D Printer – Buy Now
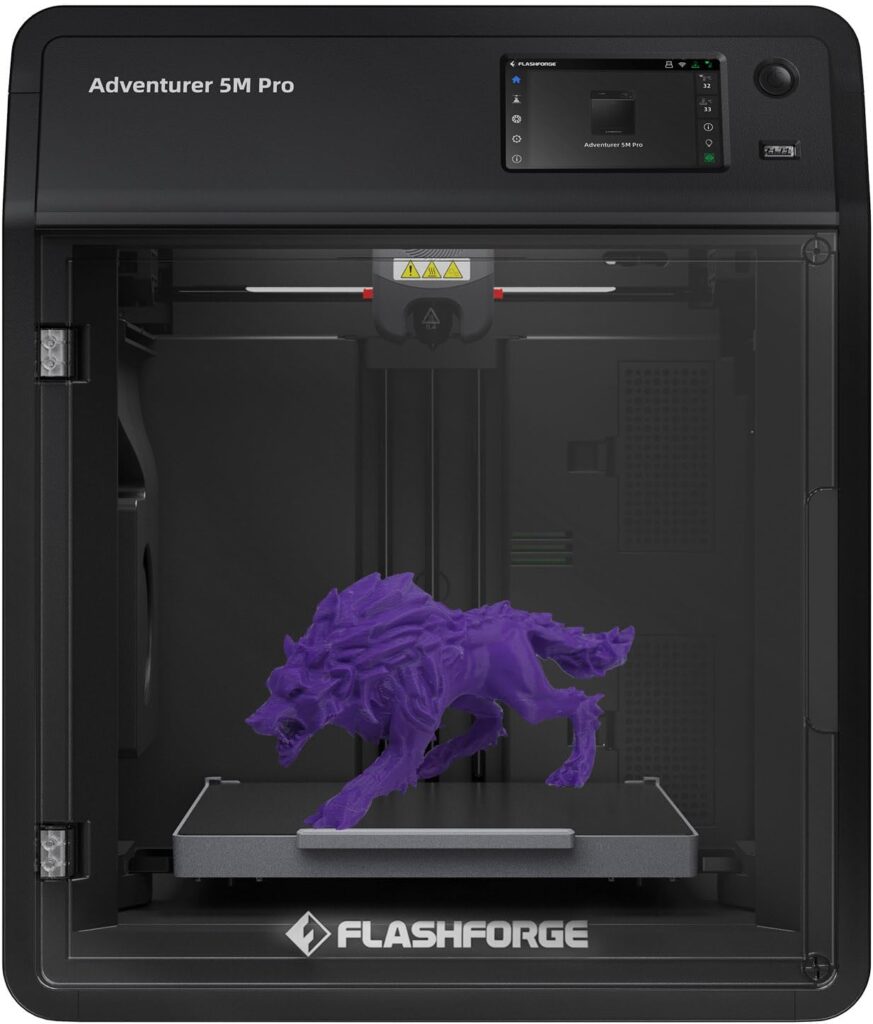
The FLASHFORGE Adventurer 5M is renowned for its user-friendly features and high-speed printing capabilities. With fully automatic leveling and a maximum printing speed of 600 mm/s, it ensures efficient and precise outputs. The 280°C direct extruder with a detachable nozzle allows for easy maintenance and versatility in material usage. Its core XY all-metal structure provides stability, and the print size of 220x220x220mm is suitable for various projects. Users appreciate its reliability and performance, making it a popular choice among professionals and hobbyists alike.
>>>Learn more about the FLASHFORGE Adventurer 5M 3D Printer<<<

The Creality K1C 3D Printer is celebrated for its impressive speed and advanced features. It offers a printing speed of up to 600mm/s and supports high-temperature printing up to 300°C, accommodating a wide range of filaments, including carbon fiber. The printer features auto-leveling and an AI camera for monitoring, ensuring precision and ease of use. Its build volume of 8.66 x 8.66 x 9.84 inches provides ample space for various projects. Users commend its robust performance and innovative capabilities.
>>>Discover the Creality K1C 3D Printer on Matterhackers – Buy Now<<<
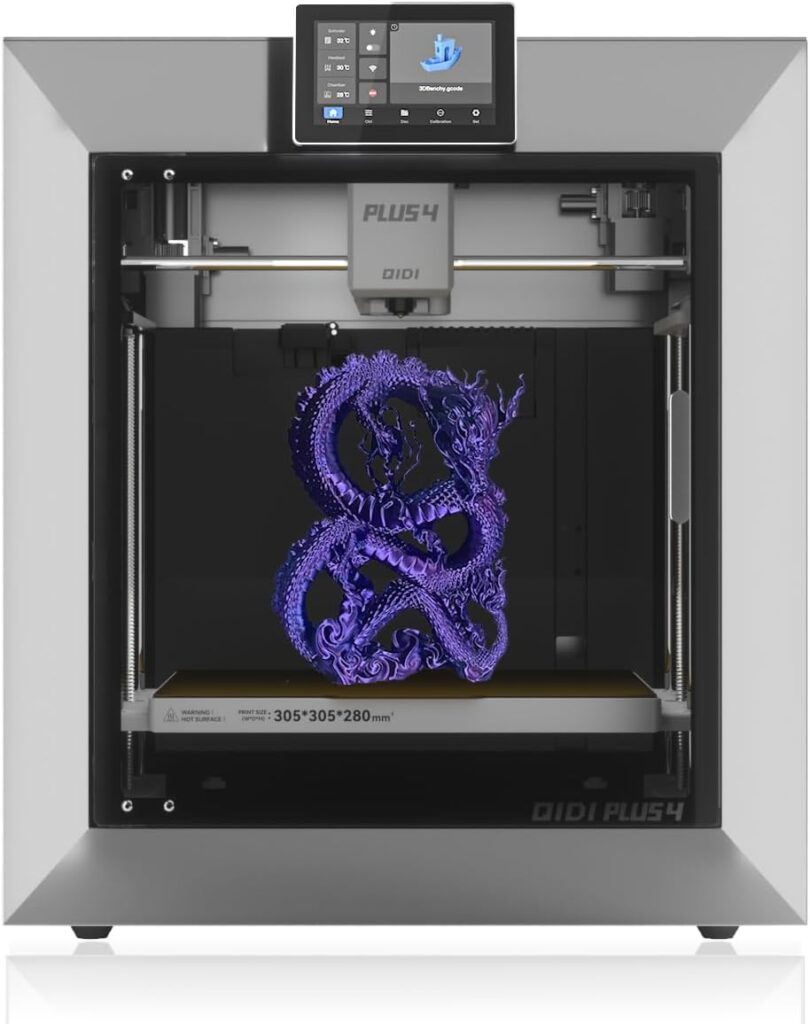
The QIDI PLUS4 3D Printer stands out with its high-speed printing and advanced temperature control. It boasts a maximum printing speed of 600mm/s and a 370°C direct extruder, allowing for the use of high-performance filaments like PPS-CF. The fully automatic leveling system and 65°C heated chamber ensure optimal printing conditions. With a large build size of 12″x12″x11″, it’s ideal for sizable projects. Users appreciate its precision and versatility, making it a valuable addition to any workshop.
>>>Explore the QIDI PLUS4 3D Printer on Amazon – Buy Now<<<
Comgrow 3D Printer Filament Dryer Box
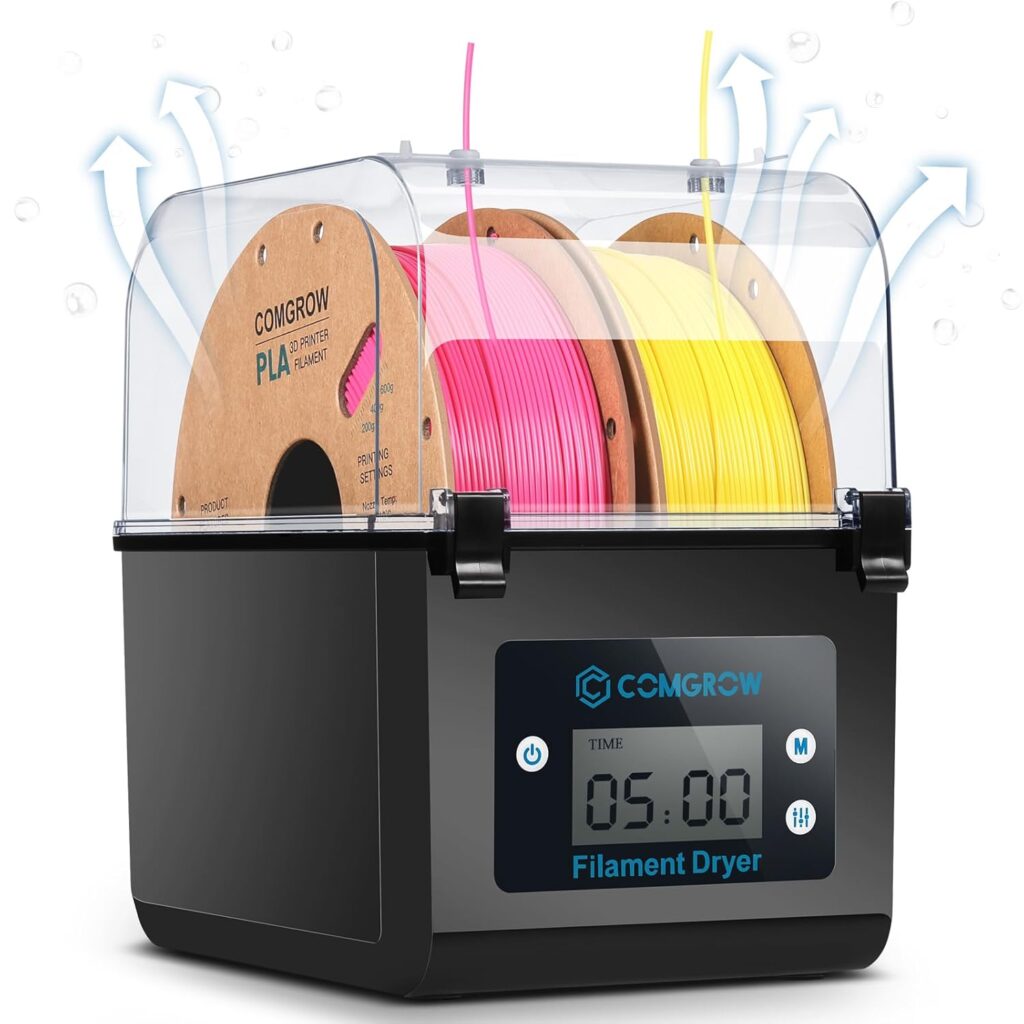
Maintaining filament quality is essential for successful 3D printing. The Comgrow 3D Printer Filament Dryer Box is designed to keep filaments dry during printing, preventing issues caused by moisture absorption. It’s compatible with 1.75mm and 2.85mm filaments, including PLA and ABS materials. Users find it effective in enhancing print quality and extending filament lifespan.
Check out the Comgrow 3D Printer Filament Dryer Box on Amazon – Buy Now
GIANTARM Silk Metallic Silver PLA 3D Printer Filament

For those looking to add a touch of elegance to their prints, the GIANTARM Silk Metallic Silver PLA Filament offers a stunning finish. With a dimensional accuracy of +/-0.03mm, it ensures high-quality results. The 1kg spool provides ample material for various projects, and users praise its smooth printing experience and eye-catching appearance.
View the GIANTARM Silk Metallic Silver PLA Filament on Amazon – Buy Now
Conclusion
The rapid advancements in 3D printing technology have made it more accessible and valuable across multiple industries. Businesses and individuals alike can now leverage 3D printing for innovation, customization, and efficiency. Whether you’re looking for a high-speed 3D printer for prototyping, a filament dryer to maintain material quality, or specialty filaments to enhance your prints, there are excellent products available to meet your needs.
As technology continues to evolve, commercial 3D printing will likely play an even bigger role in shaping the future of manufacturing, healthcare, and beyond. By investing in the right tools, you can unlock endless possibilities and stay ahead in this ever-growing field. Explore these top-rated products and take the next step in your 3D printing journey today!